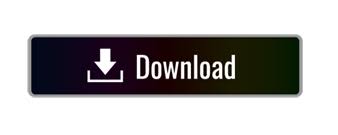

In such an arrangement, the vapour produced in the first effect can be used as a heating medium in the next effect. Two or more effects operate at progressively lower vacuums and thus with progressively lower boiling points.

To reduce the amount of steam needed, the evaporator is normally designed as a multiple-effect evaporator. It takes a large amount of energy to boil off water from a solution. The following aspects must be taken into account when planning an evaporator station: To minimize the thermal impact on the products from the heat applied, evaporation takes place in a vacuum at pressures of 160 – 320 hPa, equivalent to water boiling temperatures of 55 – 70 ☌.

As some products are sensitive to heat, the design of these systems has to be considered carefully with respect to temperature and holding time in order to achieve the desired effects on the one hand, but without causing heat damage on the other. Heat treatment is often an integral process step of an evaporator in order to achieve specific properties in the finished powder. How far the concentration process can be forced is determined by product properties such as viscosity and heat stability. The heat released during the condensing of the steam is transferred to the product via the partition.Įvaporation also constitutes the preliminary stage of the drying of the said products. Product and heating medium (steam) are kept separate from one another by means of a sheet of special steel. Water is evaporated by means of indirect heating. In the dairy industry, evaporation is used to concentrate whole milk, skim milk, whey, whey protein concentrate and permeate from membrane filtration modules. A partition is heated by hot steam and vapour evaporates from the liquid on the other side

Spreadsheets are often employed to assist with calculations associated with the analysis.General principle of evaporation. Typically, both material and energy balances are analyzed and documented by an engineer familiar with the chemical process. If the energy input from the evaporators and compressors exceeds the energy output of the condensers, the result will be poor system performance, high discharge pressure, or both. In an ammonia refrigeration system, this is accomplished by examining the sources of ammonia energy input and output: Energy Input Whereas a material balance compares the material input to output for a given process, an energy balance summarizes all energy input vs. The Industrial Refrigeration Consortium prepared a detailed explanation of this approach in Volume 15, No. compressors, condensers, evaporators, vessels, etc.), but this type of analysis is limited to the assumptions made and represent a hypothetical flow of ammonia through the process at a given load pattern. Material balances can be performed on select components (e.g. Here, the system material balance becomes trivial since the overall quantity of ammonia in the process is not changing over time. Ammonia refrigeration is an example of this type of process. Other processes use hazardous chemicals in a closed loop system where the chemical is not added to or removed from the process. In this example, the material balance would clearly document the rate at which ammonia is added to and removed from the process storage tank. The business uses the large storage vessel to fill smaller shipping and/or application containers. For example, a fertilizer distribution business may have a large anhydrous ammonia storage tank which is filled by a vendor for storage onsite. In this type of process, a material balance must summarize the names and quantities of the chemicals that are entering the process compared to the names and quantities of the chemicals/products produced by (or leaving) the process.Ĭertain processes exist for the purpose of storing a hazardous chemical and then distributing that chemical as needed. This is particularly important for processes that involve reactions in which one or more of the chemicals is consumed. The same requirement exists in the RMP and CalARP regulation except that the applicability date is J( Title 40 CFR §68.65(d)(1)(vii) and Title 19 CCR §2760.1(d)(1)(G)).Ī material balance is an assessment of the material (mass) input into a process compared to the material output. Title 8 CCR §5189(d)(3)(A)(7) and Title 29 CFR §1910.119(d)(3)(i)(G) require that “ information pertaining to the equipment in the process shall include: Material and energy balances for processes built after May 26, 1992”.
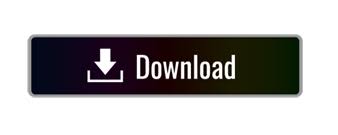